Tray Dryer & Vacuum
Vacuum Tray Dryer is a static type of dryer used in various industries under vacuum atmosphere to dry temperature sensitive materials as well as pharmaceutical and allied products. It gives complete drying and vaporization of moisture of the product. Tray drying works well for material that requires more gentle processing or cannot be atomized in an air stream due to viscosity.
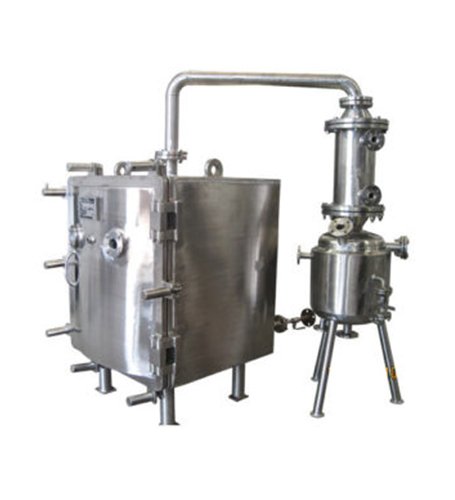
ADVANTAGE –
- It is Efficient heat sensitive
- Drying of Materials can be done in Containers
- It has Lower Drying Temperature than Standard Dryers
- Faster Drying due to Large Surface Area
- Comparatively Dries Large Moisture than Normal Dryers
- Gives High Quality Dried Material
FEATURES –
- Heating Shelfs movable system for cleaning purpose
- Solvent recovery system
- Limpet coil on vacuum chamber
- Insulation on the vacuum chamber outer surface
- Skirting
- Water heating system
TRAY DRYER –
Tray drying is a batch process used to dry materials that are liquid or wet cake. Tray drying works well for material that requires more gentle processing or cannot be atomized in an airstream due to viscosity. This dryer is well utilized for drying of wet products like crude drugs, chemicals, powders, or granules, etc. It is the most conventional dryer, used very widely and still being used where the moisture content is higher and where the product has to be dried at a low temperature for long hours.
PRINCIPLE –

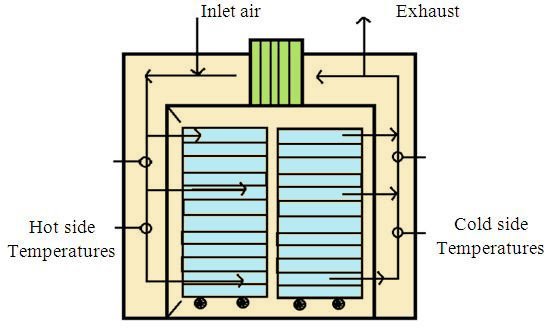
WORKING –
Tray dryer is widely used in the pharmaceutical industries. The material to be dried is placed on the trays. The heat in the dryer is produced by the heater along a side or at base. Other than the hot air generated by the oven, the other method is to employ radiator coils that use steam for heat circulation. During the heating process the material to be dried is spread out on the trays. The heated air is directed to flow in a circulation form. It flows over the material in the trays in a controlled flow. Trays can have a solid, perforated or wire mesh base. A paper lining could be used to reduce chances of contamination through contact with the tray. The efficiency of the dryer depends on recirculation of the hot air. Apart from a regular supply and presence of heated air, it also depends on supply of fresh air. The fresh air is combined with the heated air in fixed proportion for an efficient performance. Such regulated drying is important to ensure uniform drying in the dryer at the bottom as well as at the top. Apart from the double-walled construction insulation is achieved by heating coils.
CONSTRUCTION –
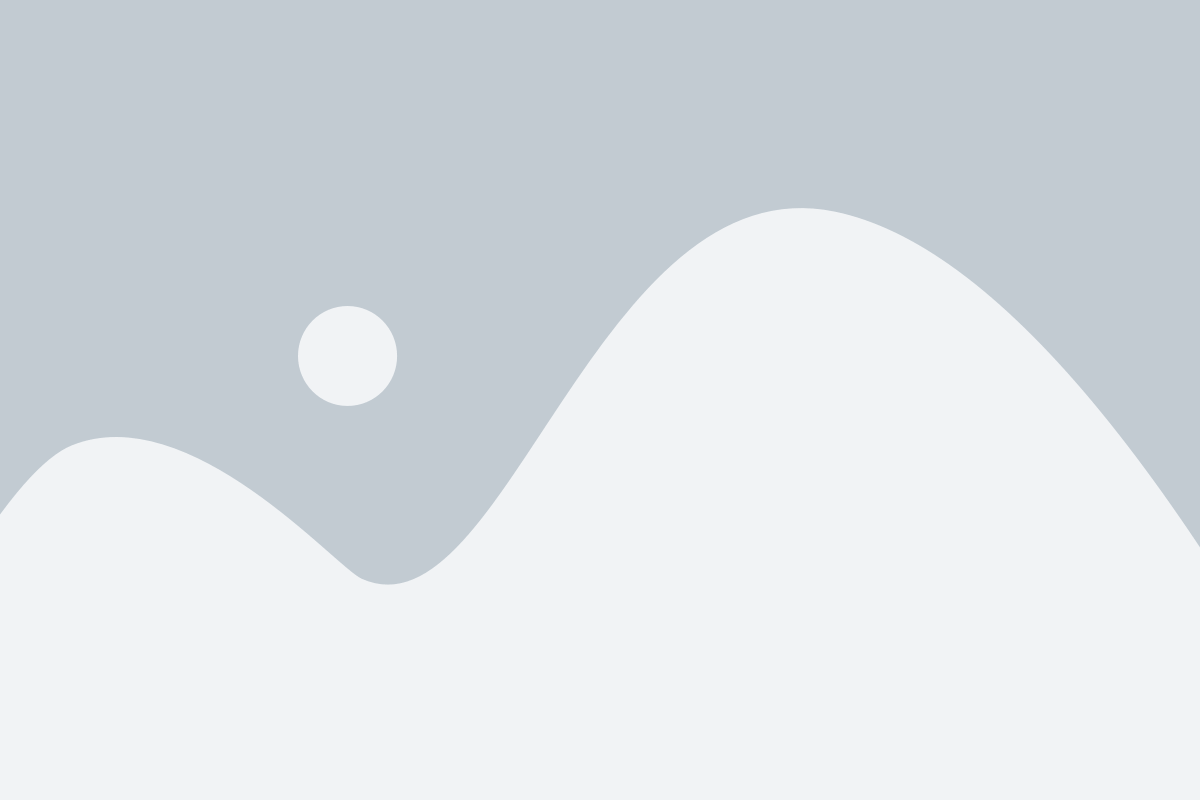